A selection of out past and current projects. Click on the headings to read more about each project.
The fossil fuel used in shipping must be replaced with renewable alternatives. Feedstock for sustainable production of biofuel will only be available in limited quantities. On the other hand, wind is a renewable energy source that is directly available to shipping in very large quantities. Shipping is also the energy user that can directly and without unnecessary energy conversion utilize wind energy most efficiently. For a transition to an energy-smart and sustainable society, it is a given that as much of the energy needed for the ship's propulsion must be taken from the wind.
For maximum utilization of available wind energy, it is required that the sail area is maximized under normal wind conditions. This sail area will be hard to handle and also dangerous at higher wind speeds. The solution is to make the sail area adjustable, for example through a telescopic arrangement. In unfavourable wind directions, it is desirable to completely eliminate the projected area against the wind, which is achieved by also making the arrangement foldable.
For more info see: Windstruc
Fastwater is a European research and demonstation project of maritime methanol fuel application, including retrofit vessels and engine development. ScandiNAOS AB participate in several parts of the project, includes:
- Development of high-speed methanol engine, which will be installed on a Swedish pilotboat.
- Detail design and enginnering for retrofitting a Swedish pilotboat into pure methanol (MD97) propulsion.
- Detail design and enginnering for retrofitting a Belgium tug vessel operated in Port of Antwerp.
For more info see: Fastwater
Bio-Met
The project is to reach Swedish climate target by 2030 - to reduce fossil emissions of fossil greenhouse gases from transport by 70%, by an alternative for shipping by retofit a small cargo vessel to run on CO2-neutral Bio-methanol. Ivar Lundh AB and Södra Skogsägarna (Södra), two parties in the project, see reduction of the environmental impact as a great importance. The bio-methanol will come from Södra's facility in Mönsterås that able to refine unused byproduct from forest industry into Bio-methanol.
In the project, a suitable vessel for the project with around 5,000 DWT / 4,000 m3 pulp-wood capacity is evaluated. After conversion, the vessel is going to sail from various ports in the Baltic’s to Mönsterås. The conversion plan includes:
- New fuel tank arrangement
- New main engine investigation
- Additional pipe and indicator system with extra safeguards to introducing methanol as a marine fuel
- Comsidering high cost of changing a new engine, a newer vessel is also evaluated as a comparison.
- Cost estimation
For more info see: SÖDRA Skogsägarna
GreenBoat
The GreenBoat project has shown concrete commercially viable methods for introducing alcohol as fuel into the workboat and recreational boat segments. Alcohols such as methanol and ethanol are identified as alternative fuels that can make a decisive contribution to improving air quality and reducing greenhouse gas emissions.
The GreenBoat project has been organized into 4 work packages where alcohol conversion has been performed for:
- A two-stroke outboard engine of older model with carburetor
- A four-stroke outboard engine of newer model with port injection
- A used recreational boat with port injected inboard engine
- A new work boat with two directly injected inboard engine
The project has shown marine petrol engines easily can be converted to alcohol fuel. The performance with alcohol fuel is the same or slightly better compared to petrol. The expected reduction in emissions have been confirmed where greater improvements are achieved on older engines than on newer ones.
For more info see: GreenBoat
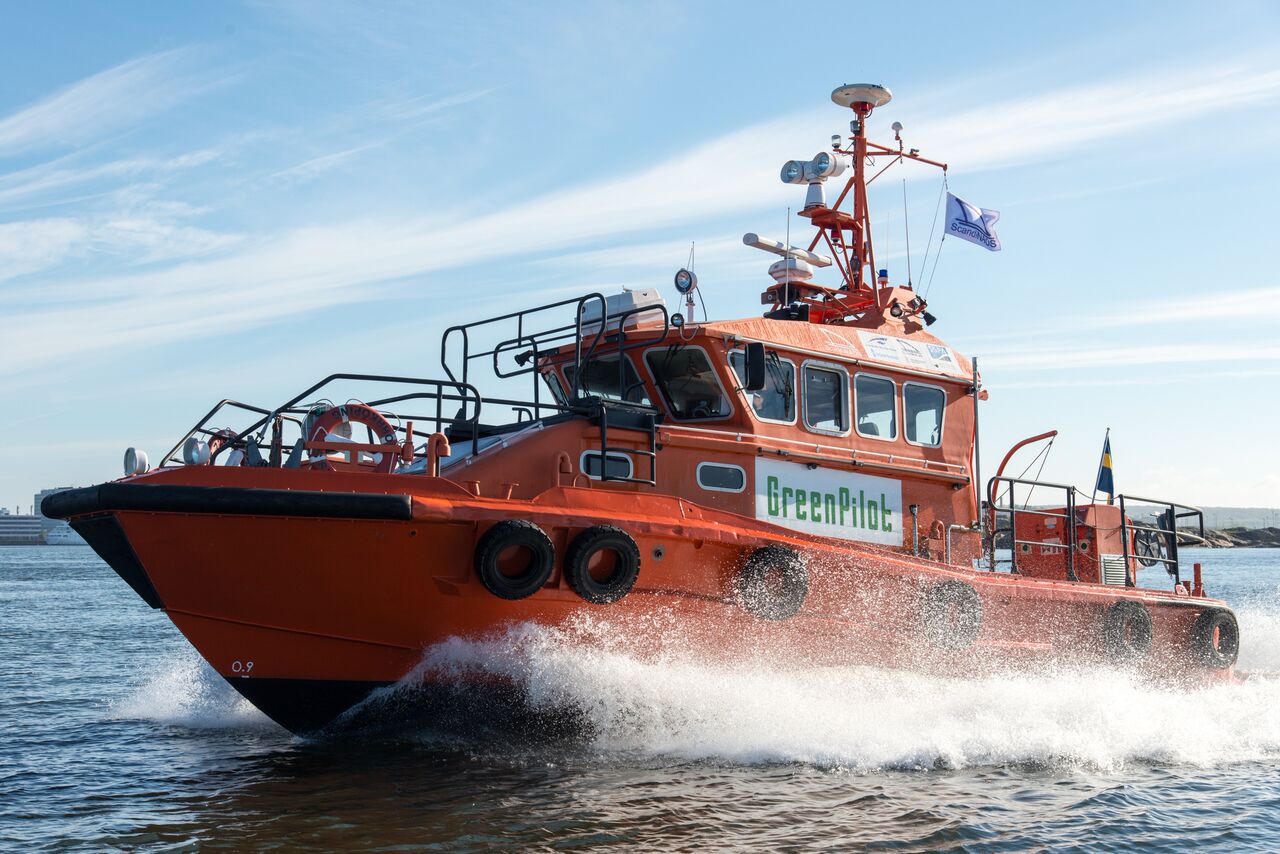
Together with the Swedish Maritime Administration (SMA) and the Swedish Maritime Technology Forum (SMTF) et al. ScandiNAOS AB is involved in a conversion project of a pilot boat. A key task in the project is to demonstrate that introduction of methanol as a fuel for smaller ships can improve competitive power and reduce the environmental impact. Other systems affecting emissions and environmental impact will be targeted as well. Examples of such systems are propulsion system, anti-fouling paint, heating, paint system, selection of material and recycling. ScandiNAOS AB is specifically responsible for identification and development of rules and regulations in addition to the design of ship conversions.
The purpose of NOVIMAR is to demonstrate the feasibility of a new transport concept based on the launch of the vessel train, or 'platooning' on the water. NOVIMAR is honored under the European Research and Innovation Framework Program: HORIZON 2020. The total grant is approximately € 8 million. Netherlands Maritime Technology (NMT) is coordinator of the project and provides project management. ScandiNAOS AB will be in charge of ship design and cargo handling.
A vessel train consists of a manned Leader Vessel with one or more Follower Vessels, which follow the Leader Vessel with highly reduced or even no crew. In addition to the cost benefits that are expected, the Vessel Train makes the use of smaller ships more profitable, so transport within urban areas can be moved from the road to the water. In addition to inland navigation, shortsea applications are also investigated.
More about the project at Netherlands Maritime Technology.
The Sustainable Marine Methanol (SUMMETH) project has the overall objective of advancing the technological development and providing recommendations for introduction of methanol as an alternative fuel for coastal and inland waterway vessels to reduce their emissions and carbon footprint. The project intends to investigate methanol combustion concepts and ship fuel systems that will lead to cost effective alternatives for ship operators to reduce their emissions and carbon footprint.
Stena Germanica Methanol Conversion
Following the Effship project where methanol was identified as a possible marine fuel and the SPIRETH project where a type of methanol system was tried on board Stena Scanrail it was decided to convert the main engines of Stena Germanica for methanol.
ScandiNAOS AB was involved in de design process from start, including arrangement, system design and overview of rules and regulations. ScandiNAOS AB has also been part of the alternative design process and procedures for methanol bunkering.
TransTimer Scrubber Retrofit
During the design and installation process for retrofitting a scrubber for TransTimber, managed by TransAtlantic Ship Management AB, ScandiNAOS AB has been involved as technical consultants for the owner. ScandiNAOS AB has also provided structure drawings, interface drawings and production drawings.
Initiated by ScandiNAOS AB with the purpose to test in full onboard scale (Stena Scanrail) and in testbed, methanol and di-methyl ether (DME) as fuel and how to handle onboard. The latter to serve as input to development of rules for highly flammable fuel onboard. Participants: ScandiNaos, SSPA, Stena, Haldor Topsoe, Lloyds, Wärtsilä, Methanex.
DESSO
Initiated by Lloyds, managed by SSPA and with participation of Chalmers,Kockum Sonic, Stena, Silja Line, Swedish Club, Kattegatt design and Globtech/Mardeq/Naos (later ScandiNAOS AB). The project was a study, in the aftermath of the Estonia disaster, how to design a ro/pax that after a severe damage could sink but do so without excessive heel and without capsizing.
Stora Enso Base Port and NETSS Projects
In 1996, the forest product company Stora (later StoraEnso) decided to implement a rail-seaborne intermodal transport system for their paper products. The base was the Stora Enso Cargo Unit (SECU), rail-car maximised, with the dimensions 3.8x3.8x13.2m and with a carrying capacity of 80 tons.
The conceptual ship design and coordination of the terminal design and handling equipment was done by Globtech. The preliminary design and class drawings was done by NAOS. The ship design with engine and superstructure forward allowed straight lanes for fast cargo handling (12000 tons could be handled in less than 1.5 hours) and even trim with min. ballast in all cargo conditions.
Three ships were built 2000 to 2001 at Flender Werft and 2006 to 2007 another three at Rauma Repola. With the “mill to terminal” SECU and the fast handling considerable savings in transport costs and less cargo damages were achieved.